Graphite's High-Temp Resistance: Melting Solutions Explained
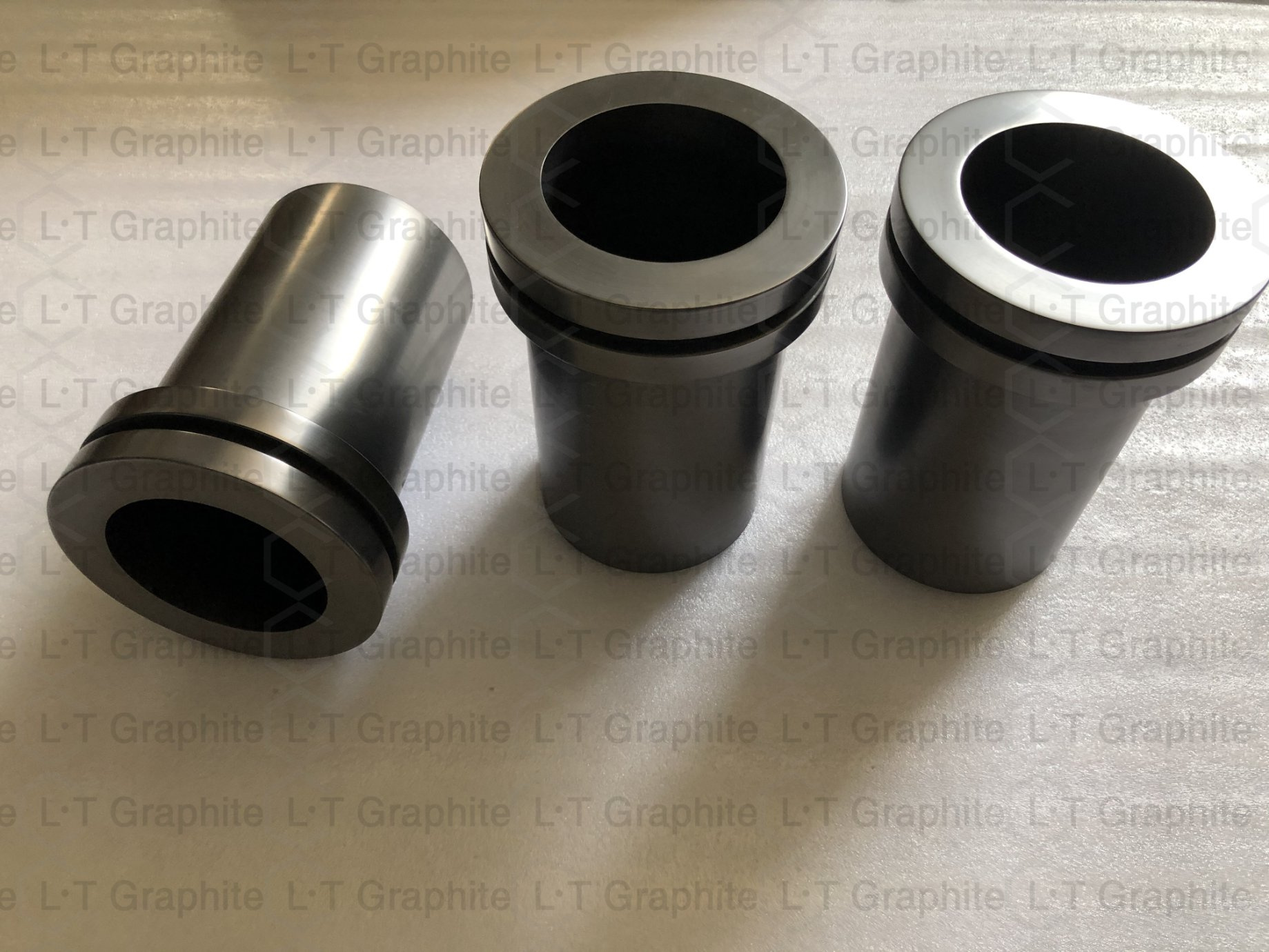
Graphite’s remarkable resistance to high temperatures isn’t just a quirk of nature—it’s a cornerstone of its utility in industries ranging from metallurgy to electronics. Unlike most materials that degrade or melt under extreme heat, graphite maintains its structural integrity up to temperatures exceeding 3,600°C (6,500°F) in inert atmospheres. This article dissects the science behind graphite’s high-temperature resistance, explores its practical applications, and examines how engineers leverage its properties to solve melting and thermal management challenges.
The Atomic Secret Behind Graphite's Heat Tolerance

Graphite’s resilience begins at the atomic level. Composed of layers of carbon atoms arranged in hexagonal rings, these layers are held together by weak van der Waals forces, while the bonds within each layer are exceptionally strong (covalent bonds). This unique structure creates a material that is:
- Thermally Conductive: Heat travels efficiently along the basal planes, dissipating rapidly.
- Anisotropic: Properties differ along and perpendicular to the layers, allowing for directional heat management.
- Chemically Inert: Minimal reactivity with most substances at high temperatures.
"Graphite's layered structure acts like a thermal shield, preventing localized heat buildup that would otherwise cause melting," explains Dr. Elena Marquez, a materials scientist at the National Institute of Standards and Technology (NIST). "Its ability to redistribute thermal energy makes it indispensable in extreme environments."
Applications Where Graphite Defies Melting

1. Metallurgical Furnaces
In steel production, graphite crucibles and electrodes operate at temperatures above 1,600°C (2,900°F). Its low thermal expansion and resistance to slag corrosion ensure consistent performance, even in molten metal environments.2. Aerospace Components
Graphite composites reinforce rocket nozzles and re-entry shields, enduring temperatures up to 2,500°C (4,500°F) during atmospheric re-entry. NASA studies show that graphite-based heat shields lose % of their mass after repeated thermal cycling.3. Electronics Manufacturing
Graphite molds shape molten silicon wafers at 1,414°C (2,577°F), the melting point of silicon. Its non-reactive nature prevents contamination, ensuring semiconductor purity.Key Takeaway: Graphite's applications in extreme heat environments are not limited to passive resistance—it actively contributes to process efficiency by minimizing thermal distortions and chemical reactions.
Comparative Analysis: Graphite vs. Alternative Materials
Material | Melting Point (°C) | Thermal Conductivity (W/m·K) | Cost per kg (USD) |
---|---|---|---|
Graphite | 3,600 | 120–200 | 15–50 |
Tungsten | 3,422 | 173 | 30–80 |
Quartz | 1,713 | 1.4 | 5–10 |
Alumina (Al₂O₃) | 2,072 | 30 | 10–25 |

While tungsten surpasses graphite in thermal conductivity, its higher density (19.3 g/cm³ vs. graphite’s 2.2 g/cm³) limits its use in lightweight applications. Quartz and alumina, though cheaper, fail at temperatures where graphite excels.
Engineering Solutions: Leveraging Graphite's Properties
Step 1: Material Selection for Specific Heat Zones
In induction furnaces, graphite susceptor plates are positioned in high-heat zones (>1,800°C), while alumina insulators are used in cooler areas to reduce costs.
Step 2: Composite Reinforcement
Carbon fiber-reinforced graphite (CFRG) combines flexibility with heat resistance. A 2022 study in *Materials Today* found CFRG withstands 50% more thermal shock cycles than pure graphite.
Step 3: Surface Treatments
Silicon carbide coatings on graphite molds reduce wear in molten aluminum casting, extending lifespan by 30–40%.
Myth vs. Reality: Common Misconceptions About Graphite

Myth: Graphite Melts at 3,600°C
Reality: Graphite sublimes (transitions directly from solid to gas) at this temperature in vacuum. In air, oxidation begins at ~700°C, but structural integrity remains until ~3,000°C.
Myth: All Graphite Grades Perform Equally
Reality: High-purity, fine-grain graphite (99.9% C) withstands 20% higher temperatures than industrial-grade (98% C) due to reduced impurities acting as thermal weak points.
Future Trends: Pushing Graphite's Limits
Researchers at MIT are developing graphene-graphite hybrids with 5x higher thermal conductivity (up to 1,000 W/m·K). These materials could revolutionize heat exchangers in nuclear reactors, where current designs operate at 30% efficiency due to thermal bottlenecks.
Can graphite be used in molten salt reactors?
+Yes, graphite moderators are used in molten salt reactors operating at 700°C. However, neutron irradiation causes gradual embrittlement, limiting lifespan to ~20 years.
Does graphite oxidize at high temperatures?
+In oxygen-rich environments, graphite oxidizes above 450°C, forming CO₂. Inert atmospheres (e.g., argon) prevent this, preserving its structure up to 3,000°C.
How does humidity affect graphite's thermal performance?
+Moisture absorption reduces thermal conductivity by up to 15% due to water molecules disrupting carbon layer interactions. Drying at 200°C for 24 hours restores performance.
"Graphite is not just a material—it's a thermal engineer's Swiss Army knife," notes Prof. Rajesh Kumar, Director of the Advanced Materials Lab at Stanford. "Its ability to adapt to extreme conditions while remaining cost-effective ensures its dominance in high-temperature applications for decades to come."
In conclusion, graphite’s high-temperature resistance is a symphony of atomic precision and engineering ingenuity. By understanding its limitations and leveraging its strengths, industries continue to push the boundaries of what’s possible in the hottest, most demanding environments on Earth—and beyond.